WE PROVIDE THE SERVICE OF OUR EQUIPMENT WITH A QUALIFIED MECHANIC REMOTELY AND WITH DEPARTURE TO THE CLIENT
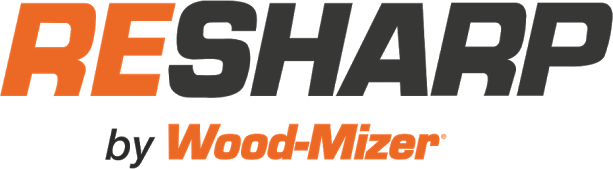
Leave saws maintenance to experts – Let experts to maintenance your saws
Many Wood-Mizer distributors offer a full range of saw sharpening services, which not only sharpens your band saws, but also completely updates them, as the saw service is performed on the same equipment used at the factory to prepare new saws. Each saw is sharpened using the best CBN sharpening technology, which ensures sawing accuracy and straight, smooth cuts.
Proper maintenance of band saws extends their service life and allows you to get products of consistently high quality.
Band saw customer support package
With this in mind, Wood-Mizer has developed a range of sharpening equipment that will satisfy owners of both basic band saws and large industrial equipment. The saw sharpening system will provide customers with almost factory results. Our equipment for sharpening and setting of band saws has been carefully designed to create a balance between inexpensive but high-quality sharpening results and long operation in difficult working conditions.
All Wood-Mizer grinding equipment uses automatic devices based on CBN sharpening technology, which provides the best sharpening results. Wood-Mizer produces its own CBN grinding wheels, which fully correspond to the tooth profile and do not require additional adjustment. Use CBN grinding wheels allows to sharpen saws to factory specifications, precisely keeping a step and height, an angle of sharpening and end of tooth.
OUR ADVANTAGES
- we sharpen the saws with CBN grinding wheels while preserving the originality of the saw tooth
- wash the saw with coolant, which gives durability and preservation of the saw blade
- we deliver the serviced cutting tool on the adjusted route to your enterprise
- we work with VAT

7 ADVANTAGES BAND SAWS Wood-Mizer®
- exact geometry of the saw
- the saws are welding on factory equipment IDEAL BAS-100
- high quality steel
- wide choice of parameters and profiles
- protection against counterfeiting (individual number of each saw, quality certificate of the manufacturer)
- special packing of saws
- every saw is ready to work
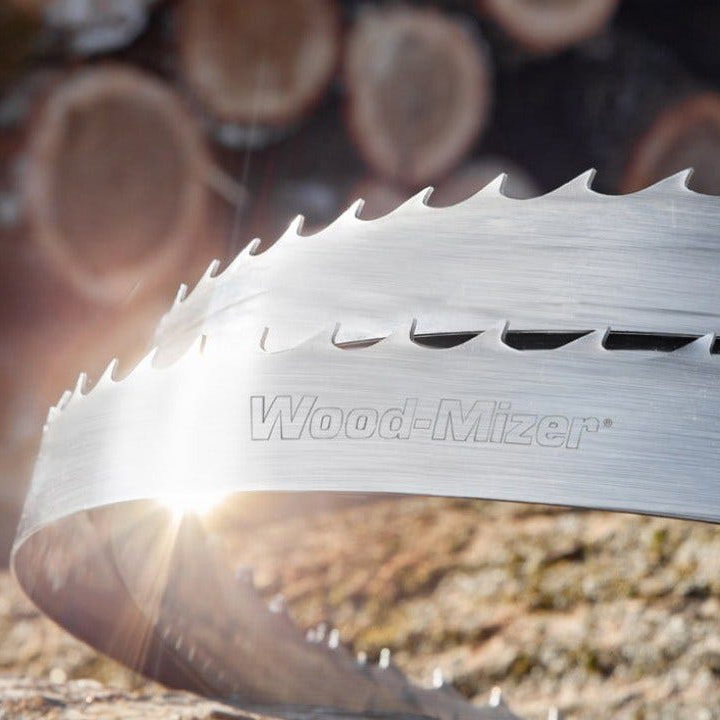
7 ADVANTAGES OF OUR MACHINES
- reliability in use, work 24/7
- operation of a log at the expense of a set of hydraulics
- speed of calculation of saw products using Electronic Setworks
- we complete machines with different types of engines: electric, petrol, diesel
- efficiency, low costs for consumables, due to high-quality original spare parts
- mobility, the ability to work on outside near the raw materials
- precision in sawing
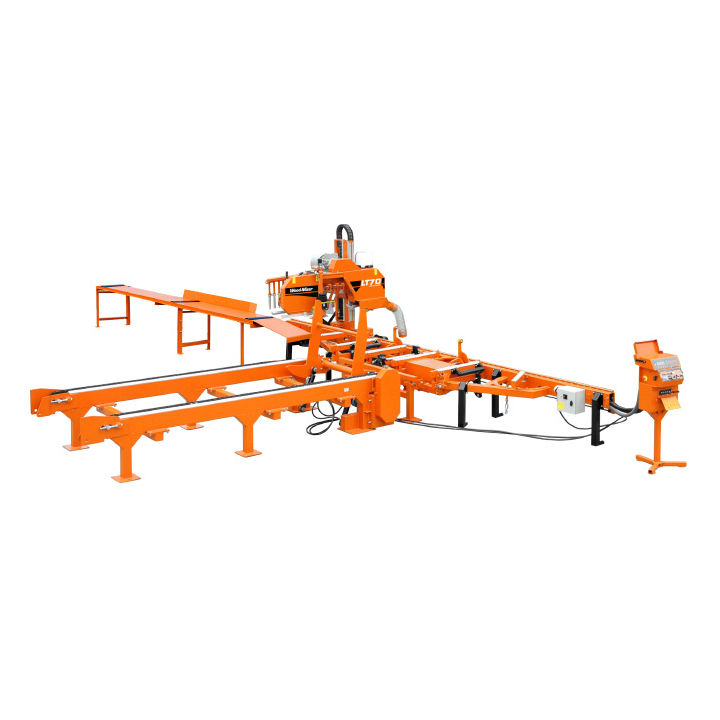
OUR PRODUCTS
SilverTIP
SilverTIP is an excellent saw for sawing both logs and beams on an industrial scale. Made of carbon steel, the SilverTIP band saw is used in mobile and stationary band saws, including horizontal separate ones. Carbon steel is one of the most common in the production of narrow band saws. These saws sharpen well, although they can withstand less sharpening than high-alloy steel blades, because the material from which SilverTIP saws are made is softer than high-alloy steel.
Width 32 mm, 35 mm, 38 mm, 40 mm, 45 mm, 50 mm, 75 mm
Thickness 1.00 mm, 1.07 mm, 1.14 mm, 1.27 mm, 1.40 mm
Profile 9/29, 10/30
DoubleHARD
DoubleHARD is a strong and versatile saw that is excellent at sawing softwood and hardwood, material with a lot of knots and resin, as well as frozen wood. DoubleHARD blades are made of high-alloy steel. The teeth of this saw undergo an induction hardening procedure, which provides them with twice as much strength and doubles the service life of the saw between sharpening compared to standard carbon steel blades.
Width 32 mm, 35 mm, 38 mm, 40 mm, 50 mm
Thickness 1.00 mm, 1.07 mm, 1.14 mm, 1.40 mm
Profile 4/32, 7/34, 9/29, 10/30, 13/29
MaxFLEX
MaxFLEX are high-quality universal band saws that have maximum flexibility. Made of high-alloy premium steel, these flexible saws have a long service life and effectively saw any wood. MaxFLEX saws are generally used in mobile and industrial woodworking plants. They are sharpened with a CBN disk and their strength corresponds to DoubleHARD band saws.
Width 32 mm, 35 mm, 38 mm
Thickness 1.00 mm, 1.07 mm, 1.14 mm, 1.40 mm
Profile 9/29, 10/30, 13/29
BiMETAL
BiMETAL are saws made of two types of high-alloy steel, and the teeth are additionally hardened. Due to their design, BiMETAL band saws stay sharp three times longer than standard carbon steel saws. BiMETAL saws have a longer service life and are designed to solve a variety of woodworking production tasks. They are sharpened with a CBN disk.
Width 34 mm
Thickness 1.07 mm
RazorTIP
RazorTIP Stellite® – band saws with stellite teeth, which demonstrate excellent wear resistance, withstand repeated sharpening and are able to work longer than standard saws, even when sawing difficult to handle tropical hardwoods. RazorTIP saws are made of high-alloy steel, the tip of the teeth is stellite. They are sharpened with help
CBN disc. Such blades do not blunt longer than ordinary hardened teeth.
Width 32 mm, 38 mm
Thickness 1.07 mm, 1.14 mm
TECHNICAL TIPS
HOW TO CORRECTLY CHOOSE A BAND SAW WOOD-MIZER
A = Tooth spacing
B = Gullet
C = Tooth height
D = Hook angle
E = Tooth set
Wood-Mizer produces band saws for sawing all types of wood, from wet softwood to dry hardwood. Given that the Wood-Mizer range includes more than 60 options for saw parameters, including 6 types of tooth profile and different combinations of blade thickness and width, which saw will be the best for your woodworking production?
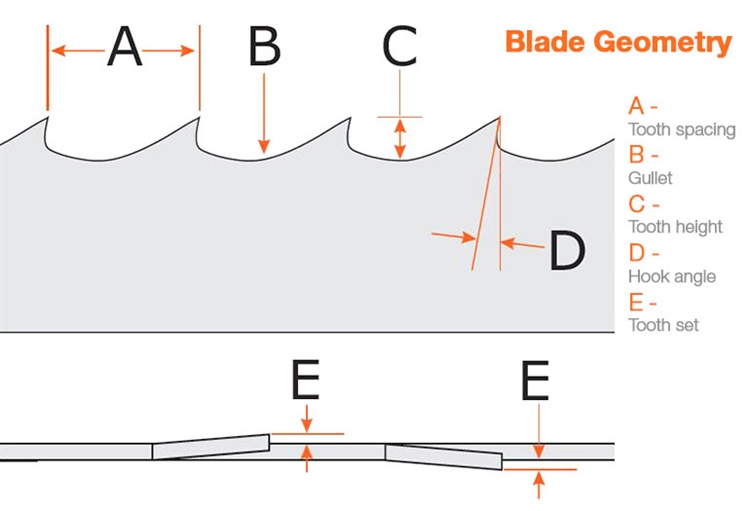
WHAT TO DO IF A “WAVE” MAKES DURING SAWING?
Many operators of machine are familiar with this problem: during sawing they get the uneven surface of a board, “wave” turns out. The problem is really serious, but it can be solved. Consistently analyze the factors that affect the sawing process. There are only four of them: operator, machine, saw, wood.
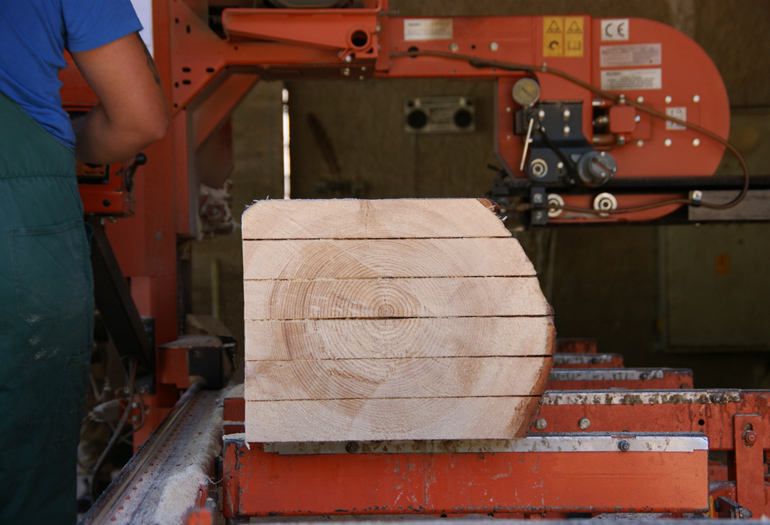
Operator
The first item on our list can sometimes be the last. After all, it depends on the operator the correct setting of the machine, the choice of sawing speed and selection of saws depending on the type of wood.
The sawing speed should be as close as possible to the maximum for this type of wood. If the sawing speed is sufficient, the surface becomes similar to a washing board. If the speed on the contrary is too high, the saw does not have time to cut and, as a consequence, there is a “wave”.
Particular attention is paid to setting up the machine. Often, even experienced operators do not pay due attention to the condition of the machine, citing the fact that the adjustment does not take much time, and maintenance of the machine is carried out once a week, or even less often. Indeed, the adjustment and repair of the machine in this case – a rather long process: after all, in a week there are many failures in the settings, which previously did not reach the hands. Our recommendation: check the settings of the machine every day, and be sure to saw the log after contact of the support rollers. Checking does not mean adjusting, and it takes a little time.
The operator must also monitor the condition of the sawmill.
Machine
Consider what parts and components of the machine can provoke a “wave” during sawing.
The guide rollers saw. They determine the position of the saw to the frame. Proper adjustment of the rollers provides additional stability of the saw in the saw. Adjustment of rollers is checked by means of an adjusting ruler which is included in the package of the machine. This ruler should be kept separate from other tools to avoid breakage. In case of loss or damage to the line, we recommend buying a new one, rather than trying to make your own.
So first let’s look at the videos. They must not have traces of working on the work surface that cause the fabric and saw to vibrate. There should be no deep scratches on the sides of the rollers that occur if the rollers do not rotate while the saw is moving. You also need to check the condition of the bearing, for which only a small backlash is allowed.
Next, check the mounting axis (finger) of the roller in the housing. In case of backlash detection (all pins which fix an axis are tightened) carry out replacement of the case. Often during operation, the place of attachment of the roller body to the guide carriage is damaged, so it is not possible to properly adjust the position of the rollers (no adjustment margin). You can try to correct the bend by dismantling the roller body. However, this damages the welding site, so it is better to replace the defective housing with a new one.
It is better to replace broken adjusting pins and twisted locknuts with new ones at once, and then, to prevent their premature failure, we recommend using only a quality adjusting tool (14 socket wrench and 3/16 ‘hexagon’).
After replacement of defective knots and details full adjustment of rollers of a saw according to the factory instruction is carried out. To ensure uniform pressure of the rollers on the saw when moving the movable roller from one extreme position to another, the guides of the movable roller must move in a plane parallel to the plane of the support table. This adjustment is often forgotten or performed incorrectly. Therefore, when adjusting the width of the cut, the stiffness of the saw blade changes, and this causes a “wave”. Also check that there is no play in the drive assembly of the movable roller guide. Even a small backlash is not allowed here.
Belts B57. Use only branded “floating” belts Wood-Mizer, as they are specially designed for belt machines. Check their condition often. If they are worn, replace them immediately with new ones to prevent the pulley rim from coming into contact with the saw, which causes premature rupture of the saw.
I washed the drink. Always use a washer to keep the saw clean. This is a simple thing that operators sometimes forget.
Adjusting the position of the saw on the working pulleys. A significant flow of saw from the pulleys leads to stretching of the rear edge of the saw, and the saw becomes unstable in the saw. In this case, the defect does not occur immediately, sometimes after the second or third sharpening, and the operator thinks that the saw is of poor quality. But the new saw after several sharpening begins to saw unstable. Bottom line: Be sure to adjust the position of the saw on the pulleys.
Installation of the machine. This is especially important in cases where the support legs of the machine are not fixed with anchor bolts, as recommended in the operating instructions of the machine. All support legs must touch the floor without any gaps. If a gap is detected, it must be removed by placing a metal plate of appropriate thickness under the support leg.
On machines that were produced before 2000, there are no middle support legs, which are installed instead of the chassis to prevent deflection of the frame when moving the cutting head. If your machine model does not have these supports, we strongly recommend that you install them yourself or at a Wood-Mizer dealer.
Saw
After making sure that all the settings of the machine meet the recommendations, we turn to the main “culprit” of the “wave”. This, of course, saw. First of all, it is important to remember that the key to success in sawing is the correct sharpening and dilution of band saws.
Most often, the “wave” occurs when sawing with blunt saws.
Insufficient dilution sharply reduces the spray speed. In addition, the saw, even if sharp enough, heats up during operation, stretches, and you need to often check its tension on the pulleys.
The sharpening angle also affects. If this angle is greater than the optimal for this type of wood, the saw is tied in the wood, and if it is not enough, the sawing speed is reduced.
Separately consider the uneven breeding. If the breeding is irregular from tooth to tooth, the “wave” will be random and will depend mainly on the uneven density of the wood. If the dilution is different for different sides of the saw blade, the “wave” will depend on the predominant amount of dilution (in one direction or another) and will occur when changing the spray speed. Indirectly, the presence of such a defect is indicated by the fact that after entering the wood, the saw dives down or up.
A saw in which the pitch of the tooth or the height of the tooth changes during the transition from tooth to tooth will saw jerkily and with considerable vibration. We must not forget about the damage caused by unresolved after sharpening burrs. In addition to increasing the risk of saw breakage, the presence of burrs leads to inhibition of saw, its heating and, accordingly, the emergence of “waves”.
Often the saw is damaged when jumping off the pulleys or when released incorrectly from the jam. This saw is usually controlled and tried to be sprayed further, but you will already get a quality saw.
Wood
Consider the characteristics of wood that affect the occurrence of “waves”.
First of all, it is an uneven density of layers. The density of the log core is usually much lower than the density of the outer layers (especially in soft woods). Therefore, the amount of saw when sawing raw materials is greater. The saw on the way passes such sites and does not cope with removal of saw from sawing. As a result, its rear part heats up and will increase in size. The saw bends in the saw and there is a “wave”. The saw profile should be selected so that it saws hard outer and soft inner layers equally well.
The occurrence of a “wave” when sawing frozen wood is well known to most operators. Completely frozen wood does not cause special problems, but sawing slightly frozen or partially frozen logs is a very difficult task. Using a saw with a profile for frozen wood solves most problems.
When sawing with a large number of knots, the risk of “waves” increases several times. Sawing in this case must be very carefully and smoothly reduced, and then just as smoothly increase the feed rate during the passage of each knot.
Sawing of very resinous wood causes special problems. The fact that the adhesion of saw and resin on the canvas saw is equivalent to increasing its thickness. And since the thickness of the saw does not change, the saw begins to rub against the walls of the saw, heat up, and, as a result, the tension drops. The “wave” occurs immediately.
Use the washing liquid in the tank for washing the saw, although this does not always help, because the native is fed only on one side of the saw, and the resin sticks to both sides.
Wood-Mizer has developed the LubeMizer system for simultaneous supply of washing liquid to both planes of the saw. We recommend purchasing this system and installing it on the machine, especially if resinous wood species are being sawn.
ABOUT US
Since the company’s founding in 1982, Wood-Mizer has manufactured and sold more than 80,000 band saws in nearly 130 countries. The great popularity of Wood-Mizer is explained by the unique design of the machine which provides accuracy of sawing, economy and reliability of the equipment.
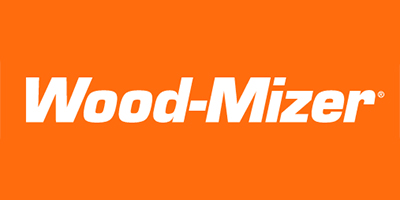